Removing slag from steel is an essential step in steel production and refining. Slag is a by-product formed from impurities in the ore, fluxes, and other materials during smelting or refining. Here’s an overview of the process:
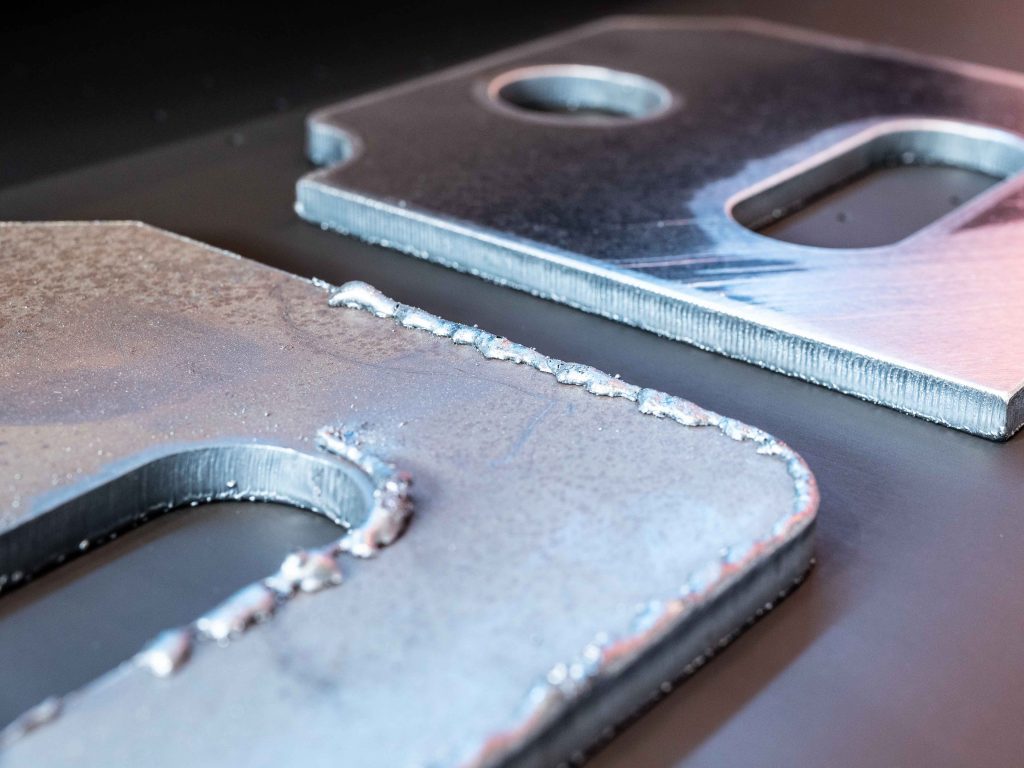
- Formation of Slag
During steelmaking, impurities such as silicon, sulfur, phosphorus, and aluminum combine with fluxing agents (like lime or dolomite) to form a molten slag layer on top of the liquid steel.
- Slag Removal Techniques
Tapping and Skimming:
After the steel has been refined in a furnace (e.g., Basic Oxygen Furnace (BOF) or Electric Arc Furnace (EAF)), the molten steel is tapped into a ladle.
The lighter slag floats on top of the steel due to density differences and is either skimmed off or poured separately.
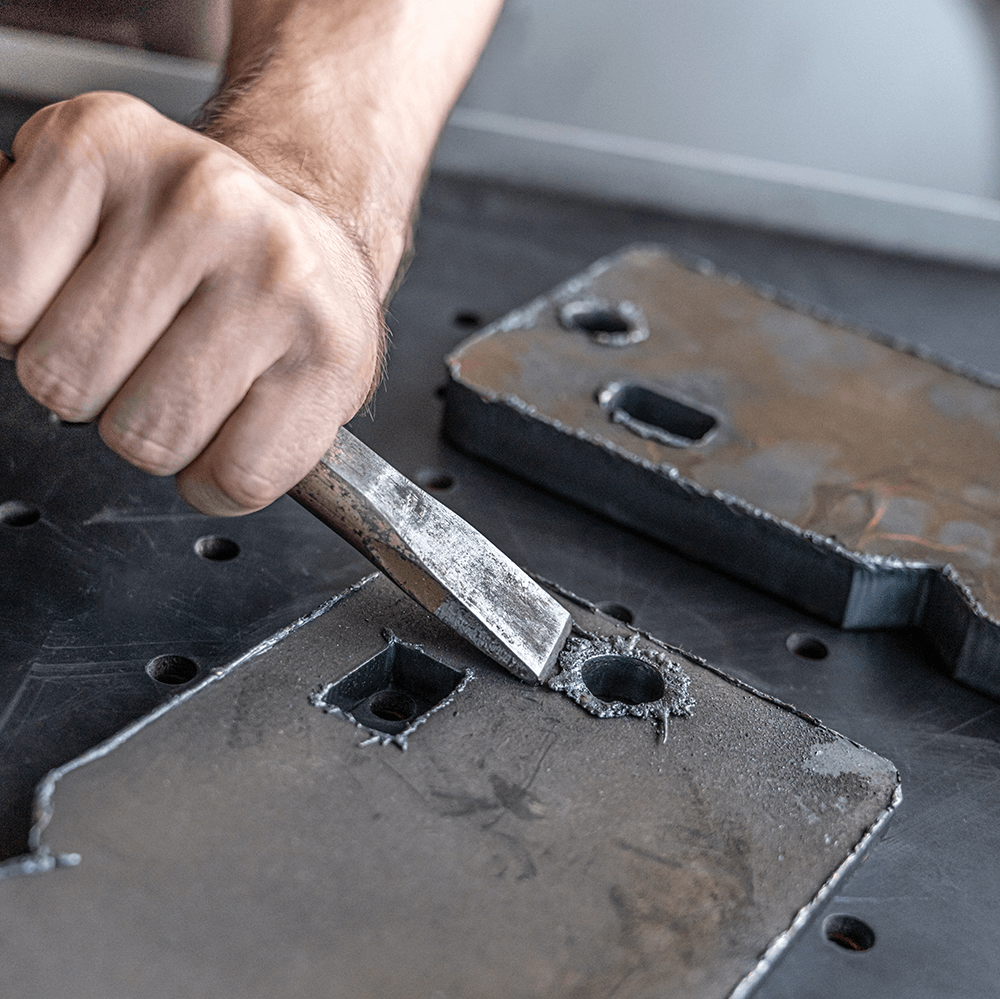
Deslagging Machines:
Specialized mechanical tools or deslagging machines are used to scrape slag from the surface of molten steel.
Slag Raking:
Manual or automated rakes are used to remove slag before casting the steel.
Flux Injection:
In some cases, additional flux materials are injected into the steel to promote slag formation and make its removal easier.
- Secondary Steel Refining
During secondary steel refining (e.g., in a ladle furnace), additional steps like stirring with argon gas or electromagnetic fields help refine the steel and remove residual slag.
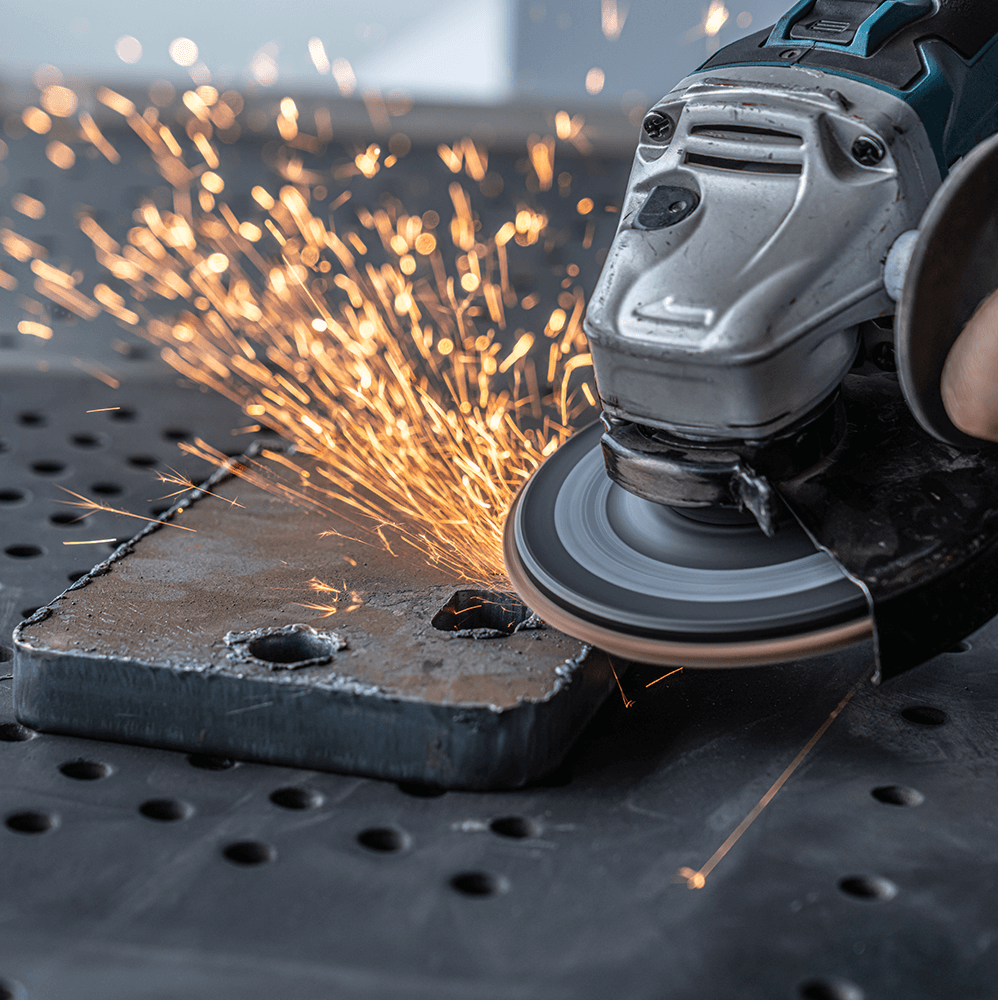
- Slag Management
The removed slag can often be processed and recycled for use in other industries, such as construction (e.g., cement production or road base materials).
Efficient slag removal is crucial for improving the quality of the steel, as it minimizes impurities and enhances mechanical properties.