The steelmaking process involves transforming raw materials like iron ore, scrap steel, and additives into steel, a strong and versatile alloy primarily composed of iron and carbon. Here’s an overview of the process:
- Preparation of Raw Materials
Iron Ore: Processed to remove impurities, often converted into pellets or sinter.
Coke: A carbon-rich material made by heating coal in the absence of air.
Limestone: Added as a flux to remove impurities during the smelting process.
Scrap Steel: Recycled steel is often added to the process for efficiency and cost reduction.
- Ironmaking
The goal is to produce pig iron, which is high in carbon and contains impurities.
Blast Furnace Method:
Iron ore, coke, and limestone are added to a blast furnace.
Hot air (often enriched with oxygen) is blown into the furnace to ignite the coke, producing carbon monoxide, which reduces the iron ore to molten iron.
The molten pig iron is tapped off and may contain up to 4% carbon.
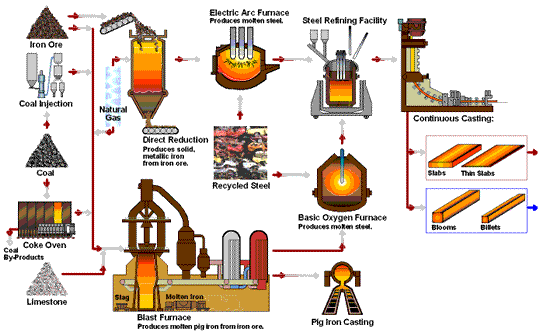
- Steelmaking
Steelmaking involves removing excess carbon and impurities from pig iron and adjusting the composition. Two main methods are used:
A. Basic Oxygen Furnace (BOF) Process
Pig iron, scrap steel, and fluxes (lime or dolomite) are loaded into the BOF.
High-purity oxygen is blown at high speed into the molten metal, oxidizing impurities (e.g., carbon, silicon, sulfur, phosphorus).
Impurities are removed as gases (e.g., CO, CO₂) or slag.
B. Electric Arc Furnace (EAF) Process
Primarily used for recycling scrap steel.
Electricity passes through graphite electrodes, generating intense heat to melt the scrap.
Alloying elements can be added to achieve desired properties.
- Secondary Metallurgy
Refines steel composition and temperature.
Processes include degassing, desulfurization, and alloy addition to improve quality.
Often performed in ladles after the primary steelmaking stage.
- Casting
Continuous Casting: Molten steel is poured into a mold to solidify into long slabs, billets, or blooms.
Ingot Casting: Molten steel is poured into molds to create large blocks.
- Forming and Shaping
Steel is reheated and rolled into final shapes, such as sheets, bars, or structural sections, in hot or cold rolling mills.
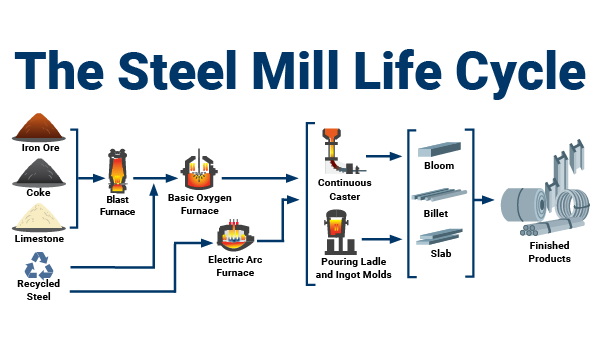
- Heat Treatment and Finishing
Steel products may undergo processes like annealing, tempering, or galvanizing to enhance properties.
Surface treatments (e.g., coating, polishing) are applied as needed.
- Quality Control
Tests are conducted to ensure the steel meets required specifications for mechanical properties, chemical composition, and surface quality.
This entire process varies slightly depending on the type of steel being made (e.g., stainless, carbon, or alloy steel) and the intended application.