The internal steel structure of a ship, often referred to as the hull structure, is critical for providing the vessel’s strength, stability, and integrity. It is composed of various interconnected components, each serving specific structural functions. Here’s an overview of how it is made:
- Material Selection:
Steel Types: The steel used is typically a specialized marine-grade steel designed to withstand the corrosive effects of seawater and provide high strength. Common types include mild steel and high-tensile steel, depending on the part of the ship and its load requirements.
- Basic Components of the Hull Structure:
Keel: The keel is the ship’s backbone, running along the bottom centerline from the bow (front) to the stern (rear). It is the first structure laid during the ship’s construction, and everything is built around it.
Frames: Frames are vertical or angled ribs that run perpendicular to the keel. They provide the ship’s primary strength and shape, acting as the skeleton onto which the hull plating is attached.
Longitudinals: These are longitudinal members running parallel to the keel, providing additional strength along the ship’s length. They are typically placed between the frames.
Stringers: Stringers are horizontal stiffeners that help maintain the overall structural integrity of the hull, working with both the frames and longitudinals.
Bulkheads: Bulkheads are vertical steel walls inside the ship that divide it into compartments. They prevent water from spreading if a section of the hull is breached and add rigidity to the structure.
Deck Beams and Decks: The deck beams support the decks of the ship. The deck itself is a key part of the structure, providing a horizontal plane that also contributes to the ship’s overall strength.
Floors: These are transverse members that run from one side of the hull to the other across the bottom. They support the bottom of the hull and help carry the loads from the keel.
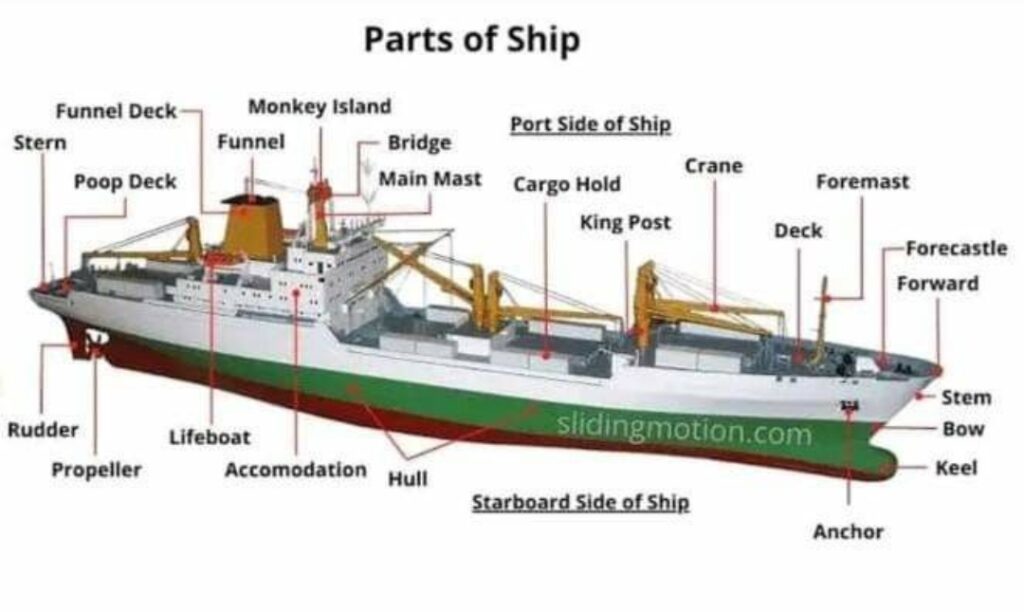
- Construction Process:
Steel Plate Cutting: Large steel plates are cut into precise shapes using CNC machines or plasma/laser cutting tools, based on the ship’s design plans.
Forming and Bending: Certain parts, like the hull plates, need to be bent into curved shapes to fit the contours of the ship. This is done through rolling or pressing the steel plates into the desired shape.
Assembly of Blocks: Ships are typically constructed using a modular block system. The ship is divided into sections (blocks), and each section is fabricated separately. This allows for parallel work, increasing the speed of construction. These blocks are assembled to form the complete structure.
Welding: The steel plates and structural components are welded together using various techniques (MIG, TIG, arc welding) to ensure a strong, watertight bond.
Internal Reinforcement: Once the hull and major structures are assembled, internal stiffeners such as girders, frames, and brackets are welded into place to enhance the ship’s structural integrity.
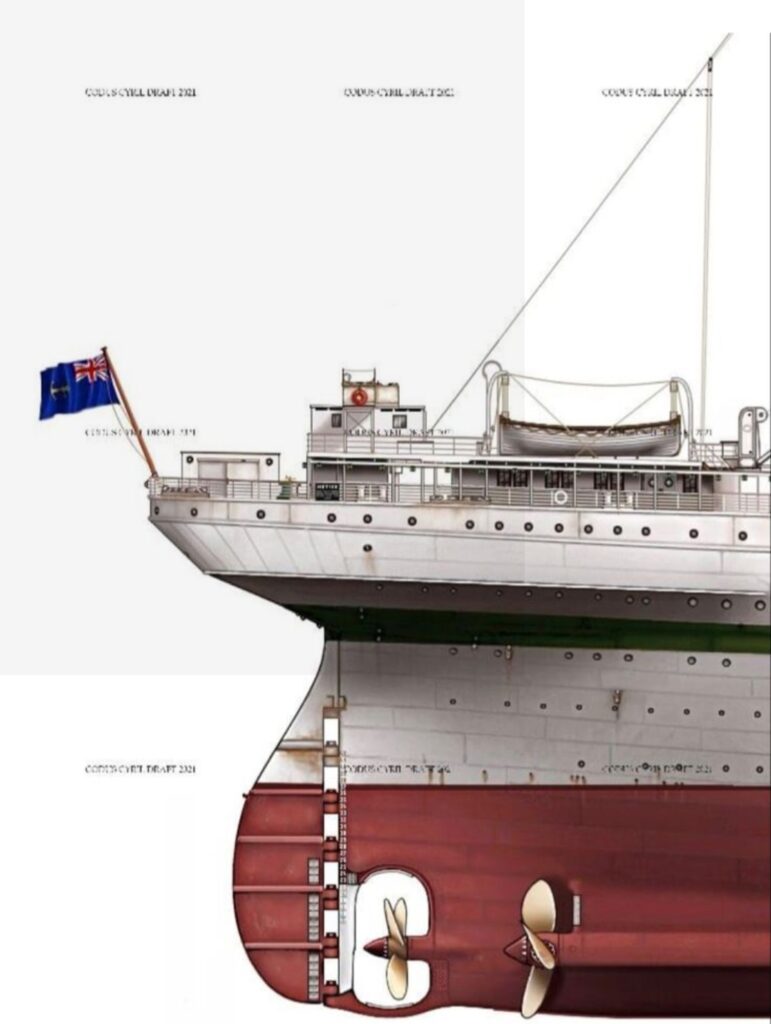
- Testing and Inspection:
Non-Destructive Testing (NDT) techniques like X-ray and ultrasound are used to ensure there are no defects in the welds or materials. Stress testing and simulation models may also be performed to ensure the ship can withstand the forces it will encounter at sea.
- Finishing Touches:
Once the steel structure is completed, the ship undergoes processes like painting and coating to protect the steel from corrosion and enhance its longevity.
Overall, building the internal steel structure of a ship is a highly coordinated effort, involving advanced engineering, material science, and skilled labor to ensure safety and performance at sea.