Blister steel is an early form of steel produced by a process called cementation, which was developed in the 17th century. This process involved heating wrought iron bars in a sealed furnace in the presence of carbon materials like charcoal. Over a prolonged period, the iron absorbed carbon, transforming it into steel.
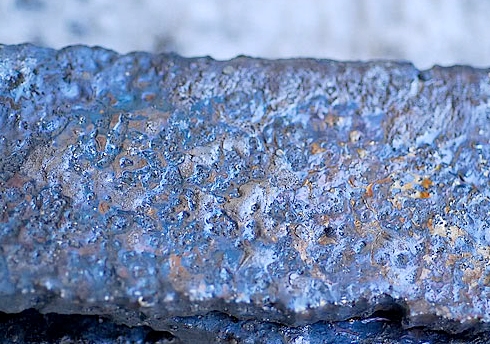
Key Features of Blister Steel:
- Appearance: It is called “blister steel” because of the blister-like marks on its surface, formed by the release of gases during the carbon absorption process.
- Carbon Content: The steel had a relatively high but inconsistent carbon content, making it less uniform than modern steel.
- Production Process:
Wrought iron bars were placed in a sealed container with carbon-rich materials like charcoal.
The furnace was heated to high temperatures for several days or weeks, allowing the carbon to diffuse into the iron.
The resulting material was steel, but the surface often showed blisters due to trapped gases.
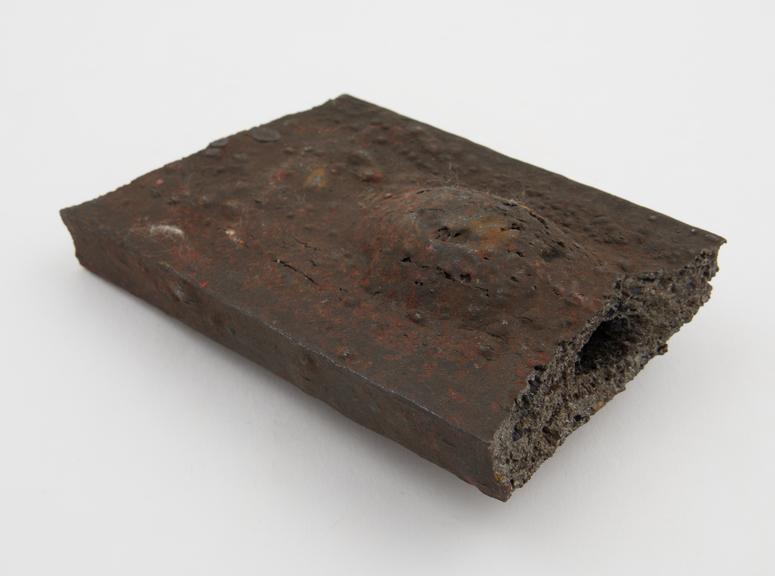
- Uses: It was used primarily for making tools, cutlery, and springs due to its improved hardness and durability compared to wrought iron.
Blister steel was later refined into crucible steel, which had a more uniform carbon distribution, through melting and further processing. These advancements marked significant steps in the development of modern steelmaking techniques.