The forming of steel involves shaping it into desired forms and structures, such as sheets, bars, or intricate components, through various mechanical processes. The principles of steel forming can be broadly categorized into the following aspects:
- Material Properties and Behavior
Plasticity: Steel must undergo plastic deformation, where it permanently changes shape without breaking.
Ductility: Steel’s ability to elongate or deform without fracturing is crucial for forming processes.
Elastic Limit: The force applied must exceed the material’s elastic limit for permanent deformation.
Work Hardening: Steel strengthens as it is deformed, requiring higher forces for continued shaping.
- Forming Methods
Steel forming processes can be grouped into hot forming and cold forming:
Hot Forming (High-Temperature Processes):
Conducted above the recrystallization temperature (around 1,100–1,300°C for steel).
Advantages: Easier deformation, reduced work hardening, and stress relief during forming.
Common methods: Rolling, forging, hot extrusion, and hot pressing.
Cold Forming (Room or Low-Temperature Processes):
Performed below recrystallization temperature.
Advantages: Higher precision, better surface finish, and enhanced strength due to work hardening.
Common methods: Cold rolling, bending, stamping, and drawing.
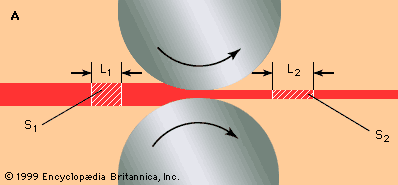
- Types of Deformation
Compression: Processes like forging, rolling, and extrusion involve compressive forces to reshape steel.
Tension: Stretching processes, such as wire drawing or sheet stretching, rely on tensile forces.
Shear: Used in processes like cutting, punching, or shearing to remove excess material.
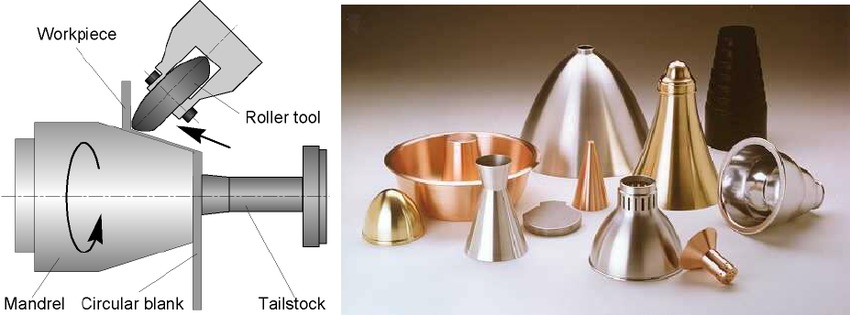
- Process Variables
Temperature: Dictates whether forming is hot or cold and influences steel’s flow stress.
Force and Pressure: Proper calculation ensures efficient deformation without causing material failure.
Strain Rate: The speed of deformation impacts energy consumption, material flow, and final properties.
Tooling and Lubrication: High-quality dies, molds, and lubrication are essential to minimize friction, wear, and defects.

- Control of Defects
Avoiding Cracks: Maintain appropriate temperatures and deformation rates to prevent cracks.
Surface Quality: Use proper tooling and lubrication to ensure a smooth finish.
Dimensional Accuracy: Monitor tool wear and ensure uniform deformation.
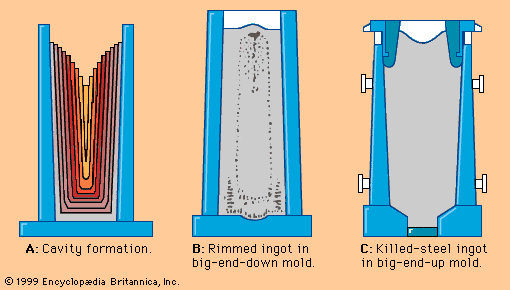
- Applications
Steel forming is critical in industries such as:
Automotive (frames, panels).
Construction (beams, reinforcements).
Machinery (shafts, gears).
Packaging (steel cans).
By understanding these principles, engineers can optimize steel forming processes to meet specific design and functional requirements.