Casting of steel is a manufacturing process in which molten steel is poured into molds to solidify into a desired shape. It is widely used to produce various parts and components with complex geometries, which would be difficult or expensive to create using machining or forging processes. Steel casting is commonly used in industries such as automotive, construction, and machinery manufacturing.
Key Steps in Steel Casting:
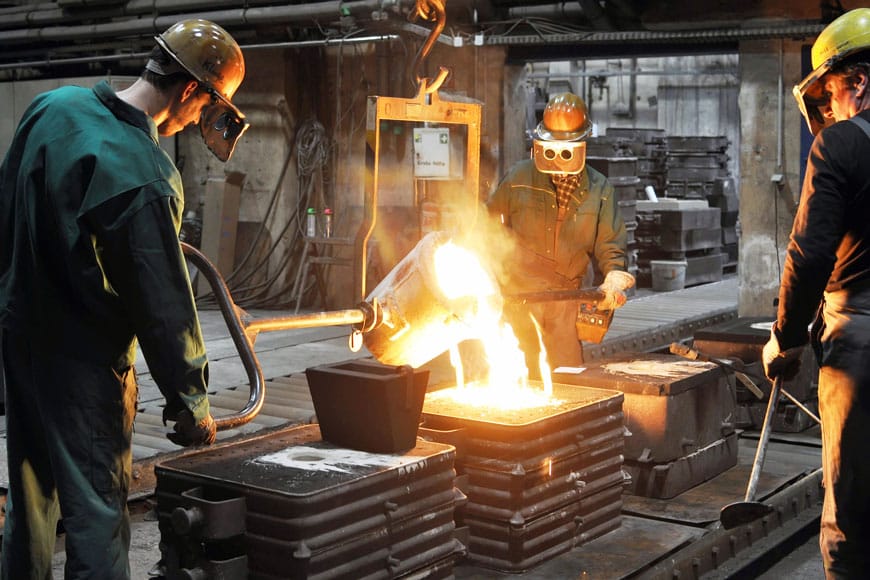
- Melting:
Steel is melted in furnaces such as electric arc furnaces (EAFs), induction furnaces, or open-hearth furnaces.
Alloying elements are added to achieve the desired chemical composition.
- Mold Preparation:
Molds are made from materials like sand, ceramic, or metal.
Sand molds are often used for intricate shapes, while permanent molds (made of metal) are used for high-volume production.
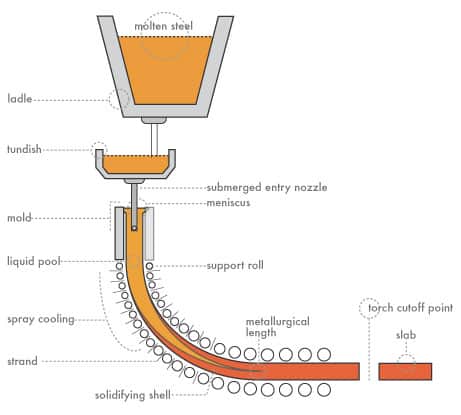
- Pouring:
The molten steel is poured into the prepared mold either manually or using automated systems.
The pouring process must be controlled to avoid defects like inclusions, porosity, or shrinkage.
- Solidification:
The steel cools and solidifies in the mold.
Solidification rate is crucial as it affects the grain structure and properties of the steel.
- Shakeout and Removal:
Once the steel solidifies, the mold is broken or opened to extract the casting.
For sand casting, the sand mold is typically broken apart.
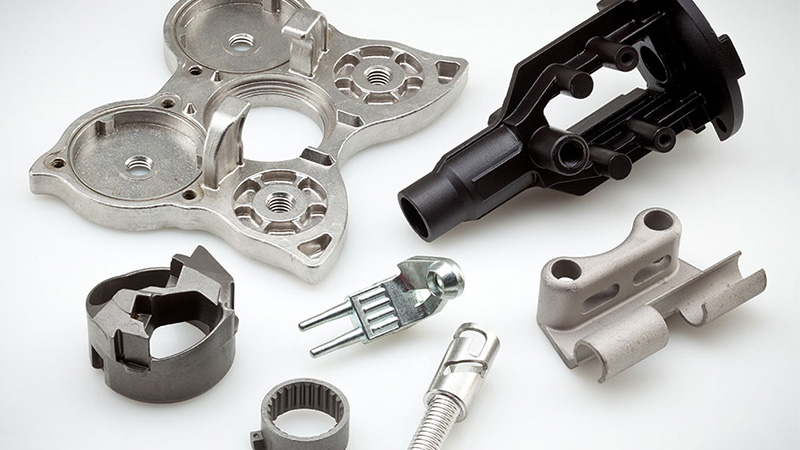
- Heat Treatment:
The casting may undergo heat treatment processes like annealing, normalizing, or quenching to enhance its mechanical properties.
- Finishing:
The casting is cleaned, machined, and inspected for quality.
Processes like grinding, polishing, and painting may be applied depending on the end-use requirements.
Types of Steel Casting Processes:
- Sand Casting:
Economical for small batches or complex shapes.
Versatile but may require more finishing work due to surface roughness.
- Investment Casting:
High precision and smooth surface finish.
Best suited for small, detailed parts.
- Die Casting:
High-speed process used for high-volume production.
Requires permanent molds and is limited to low-carbon steels.
- Continuous Casting:
Produces billets, slabs, and blooms directly from molten steel.
Used in large-scale steel production for uniform quality.
Advantages of Steel Casting:
Ability to create complex geometries.
High strength and toughness.
Wide range of alloy options for specific properties.
Suitability for both small and large-scale production.
Challenges in Steel Casting:
Potential for defects such as porosity, shrinkage, or cracking.
High energy and material costs.
Strict control needed over cooling rates and composition.
If you need further details about a specific casting technique or its applications, let me know!