A furnace steel plant is a facility designed for the production of steel by processing raw materials such as iron ore, scrap steel, and additives in furnaces. These plants are the backbone of the steel manufacturing industry and operate using various furnace technologies, depending on the scale of production, the desired steel properties, and the raw materials used.
Key Components of a Furnace Steel Plant:
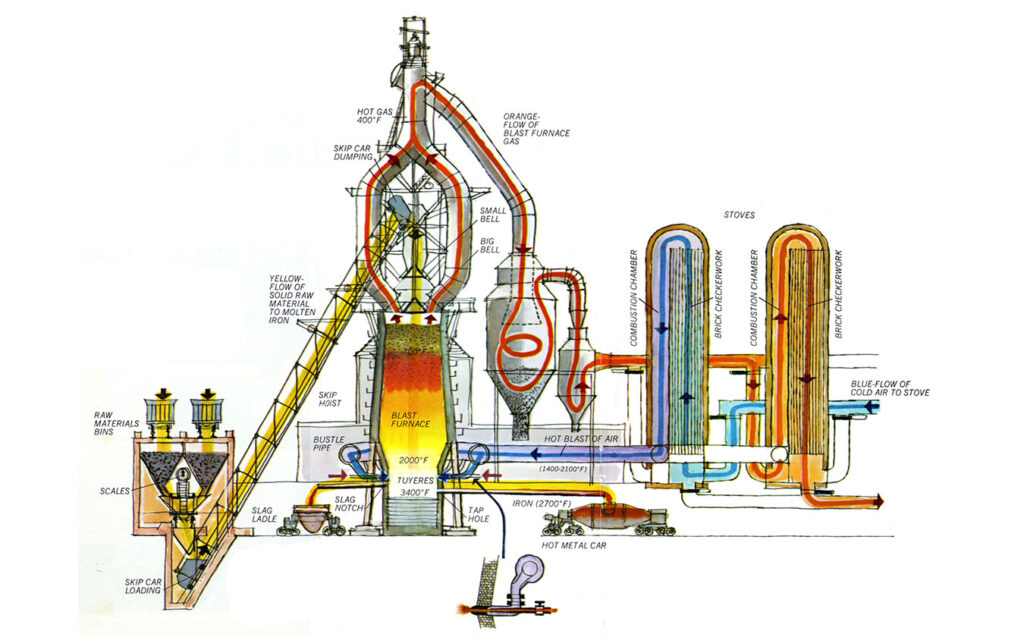
- Blast Furnace:
Used for producing pig iron from iron ore.
Iron ore, coke (carbon source), and limestone are melted together to produce molten iron.
The molten iron is transferred to a basic oxygen furnace for steelmaking.
- Electric Arc Furnace (EAF):
Mainly used for recycling scrap steel.
Uses high-power electric arcs to melt scrap metal and other raw materials.
Energy-efficient and ideal for smaller plants.
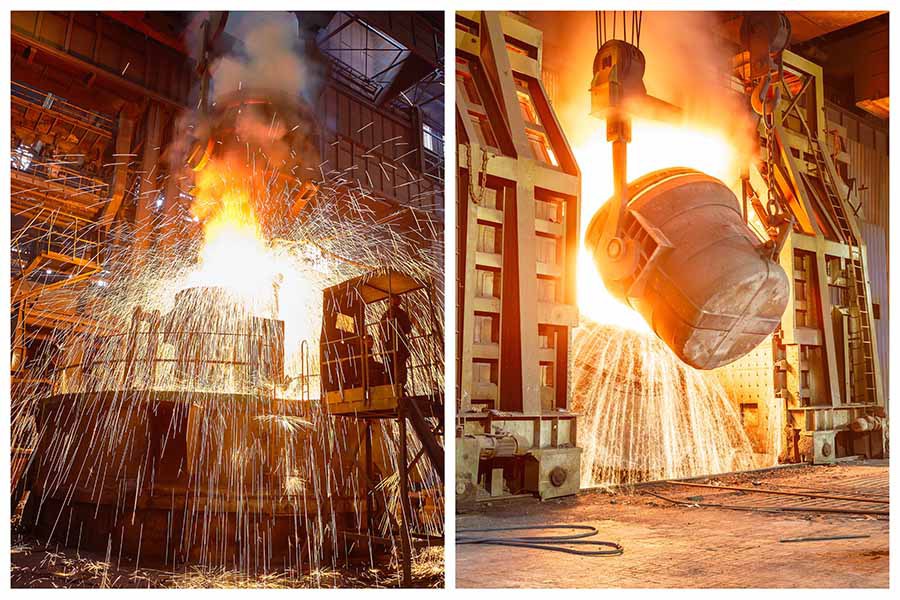
- Basic Oxygen Furnace (BOF):
Used to convert molten pig iron and scrap steel into high-quality steel.
Oxygen is blown through the molten material, reducing carbon content and impurities.
- Continuous Casting:
Converts molten steel into semi-finished products like slabs, billets, or blooms.
This step is critical for shaping and refining the steel.
- Rolling Mills:
Further process semi-finished products into finished goods like sheets, bars, rods, and beams.
Types of Furnace Steel Plants:
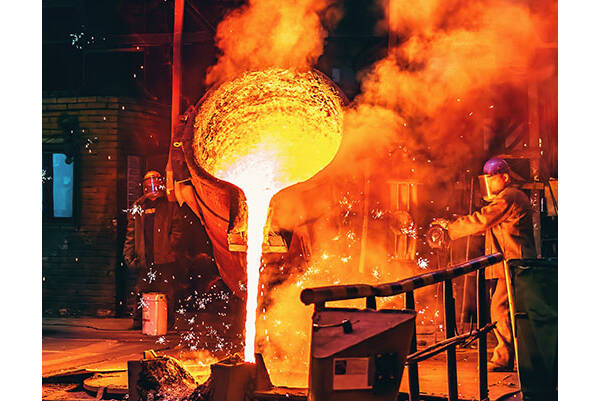
- Integrated Steel Plants:
Handle all processes from raw materials to finished products.
Use both blast furnaces and BOFs.
- Mini-Mills:
Focus on steel recycling using EAFs.
Typically produce steel for specific applications with less environmental impact.
Applications:
Steel produced in these plants is used in industries like:
Construction (rebar, beams, roofing sheets)
Automotive (frames, panels, machinery)
Energy (pipelines, turbines)
Appliances (refrigerators, washing machines)