Tool steels are a group of carbon and alloy steels specifically designed for making tools. These steels are known for their hardness, wear resistance, toughness, and ability to retain a sharp cutting edge even under extreme conditions like high heat or repeated stress. Tool steels are often used in cutting, shaping, forming, and machining applications.
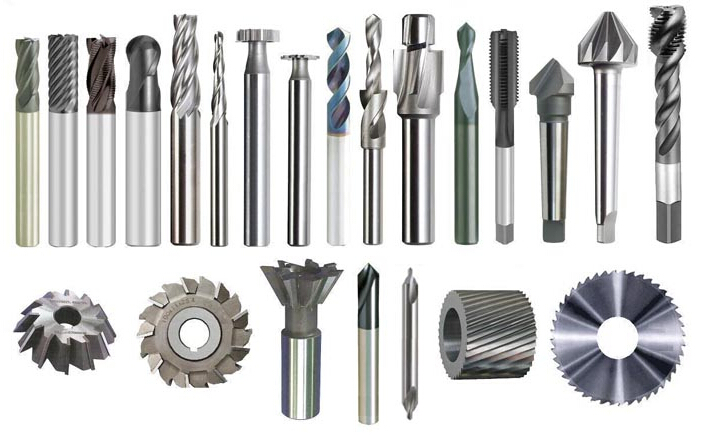
Key Characteristics of Tool Steels
- High Hardness: Achieved through heat treatment.
- Wear Resistance: Suitable for applications with significant friction or abrasion.
- Toughness: Resists breaking or chipping under stress.
- Heat Resistance: Maintains properties at elevated temperatures.
- Machinability: Can be shaped and formed before hardening.
Types of Tool Steels
Tool steels are categorized into six main types based on their composition and applications:
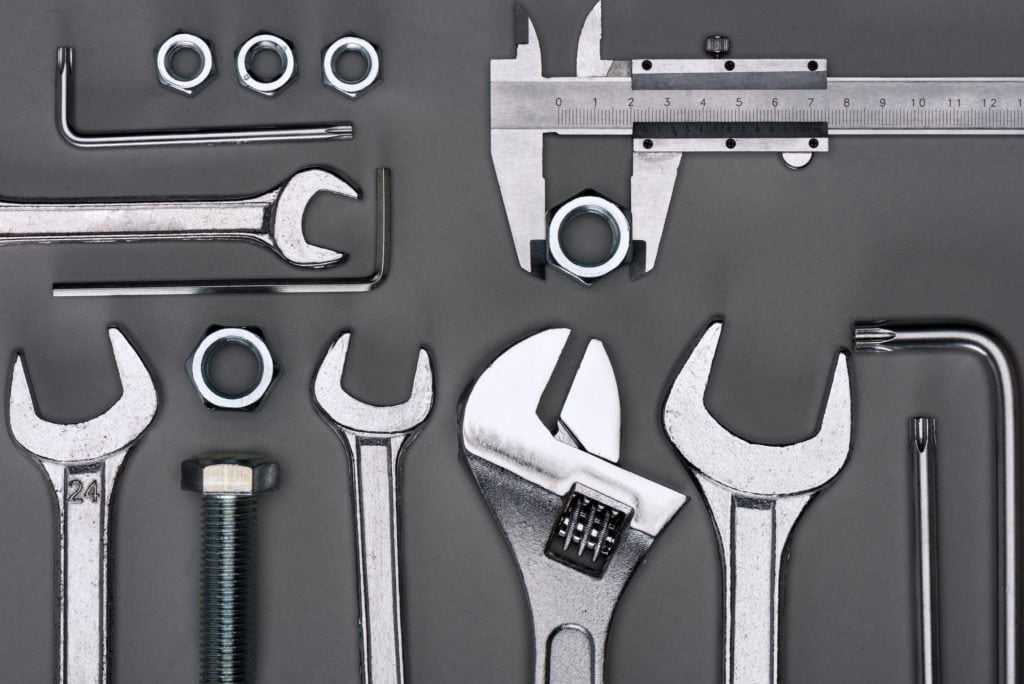
- Water-Hardening (W-series):
Simple carbon steels.
Hardened using water quenching.
High hardness but less toughness.
Used in basic tools like cutting dies and chisels.
- Cold-Work (O, A, and D-series):
Used for tools operating at room temperature.
Subcategories:
O-series (Oil hardening): Good dimensional stability, medium wear resistance.
A-series (Air hardening): Better machinability and resistance to cracking.
D-series (High carbon, high chromium): Excellent wear resistance.
- Hot-Work (H-series):
Designed for tools exposed to high temperatures (e.g., forging, casting).
High toughness and thermal resistance.
Examples: H13, widely used for die-casting and extrusion dies.
- Shock-Resisting (S-series):
High toughness to withstand sudden impacts.
Commonly used in hammers, chisels, and punches.
- High-Speed Steel (T and M-series):
Maintains hardness and cutting edge at high temperatures.
Used in cutting tools like drills, taps, and end mills.
Examples: T1 (tungsten-based), M2 (molybdenum-based).
- Special-Purpose Steels:
Steels with unique properties tailored for specific applications, like low alloy or corrosion-resistant tool steels.
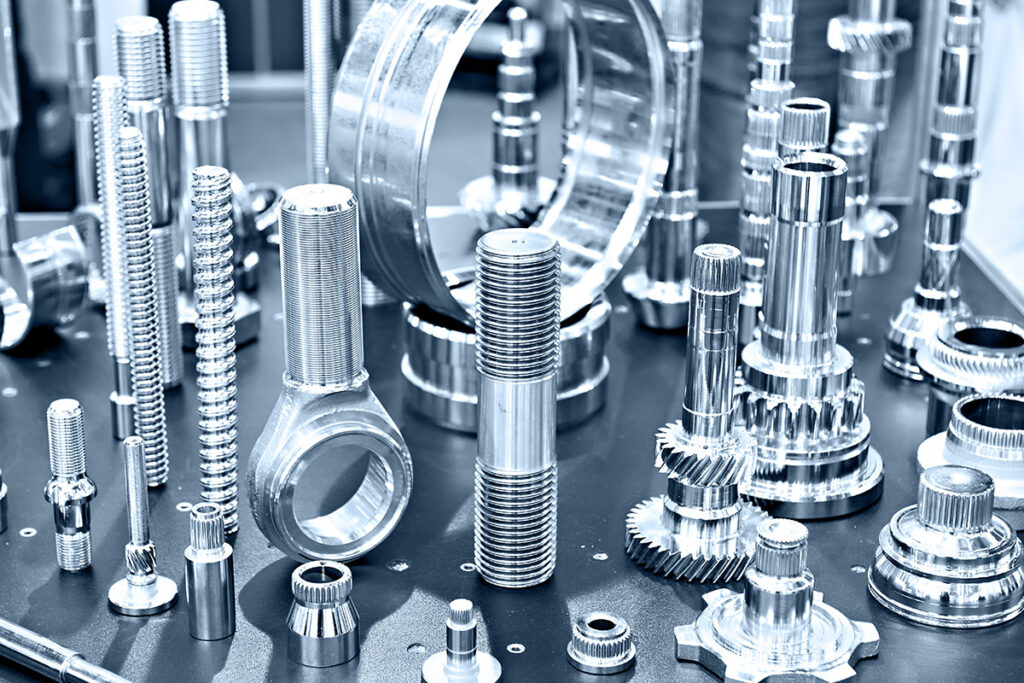
Common Applications
Cutting tools: Drill bits, saw blades, and reamers.
Molds and dies: For shaping plastics, metals, and ceramics.
Machine parts: Bearings, punches, and anvils.
Hand tools: Hammers, screwdrivers, and pliers.
Heat Treatment of Tool Steels
Heat treatment plays a crucial role in enhancing tool steels’ properties. The process involves:
- Annealing: Softens the steel for machining.
- Hardening: Increases hardness by quenching.
- Tempering: Reduces brittleness while maintaining hardness.
Tool steels are essential in manufacturing due to their durability and versatility. Their specific composition and treatment are carefully selected based on the tool’s intended use.