High-strength low-alloy (HSLA) steels are a class of steels designed to provide enhanced mechanical properties and resistance to atmospheric corrosion compared to conventional carbon steels. They achieve these properties through the addition of small amounts of alloying elements (usually less than 5% by weight). These steels are widely used in applications requiring high strength, good toughness, and reduced weight.
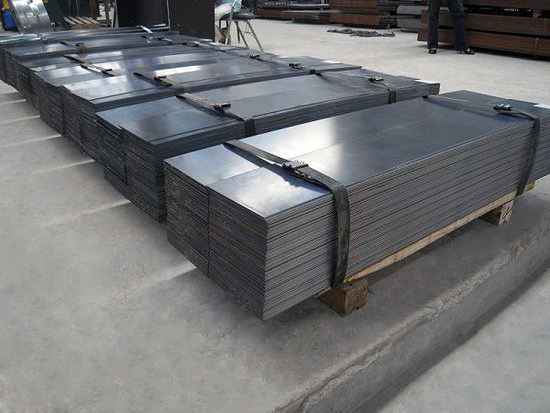
Key Features of HSLA Steels
- High Strength
HSLA steels typically have a yield strength ranging from 250 MPa (36 ksi) to over 700 MPa (100 ksi). This allows them to be used in structural applications with thinner sections, reducing weight. - Good Ductility and Toughness
Despite their high strength, HSLA steels retain good ductility and impact resistance, making them suitable for applications under dynamic loads or extreme conditions. - Improved Corrosion Resistance
Alloying elements such as copper, chromium, nickel, and phosphorus enhance resistance to atmospheric corrosion, making HSLA steels suitable for outdoor structures. - Formability and Weldability
HSLA steels are designed to be easy to form and weld, making them versatile in various manufacturing processes. - Cost-Effectiveness
Compared to traditional alloy steels, HSLA steels are more cost-effective due to their lower alloy content and reduced material weight requirements.
Common Alloying Elements
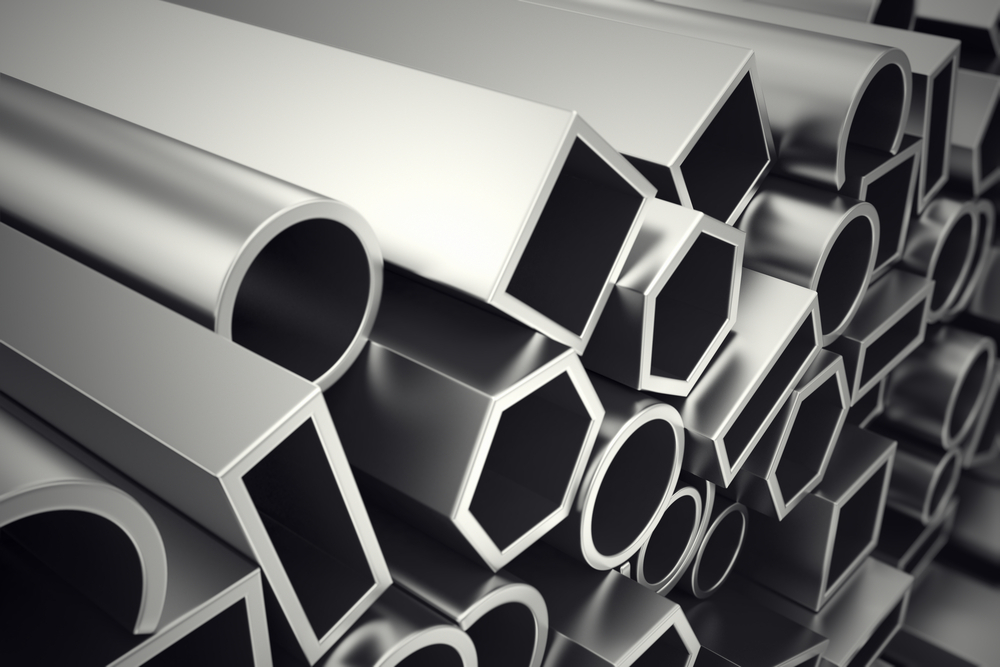
Manganese (Mn): Improves toughness and hardenability.
Vanadium (V): Enhances strength through grain refinement and precipitation hardening.
Niobium (Nb): Contributes to grain refinement and precipitation strengthening.
Titanium (Ti): Aids in grain refinement and improves toughness.
Copper (Cu): Enhances corrosion resistance.
Phosphorus (P): Improves corrosion resistance but should be used in low amounts to avoid brittleness.
Common Grades of HSLA Steels
- Weathering Steels (e.g., COR-TEN): Designed for improved corrosion resistance in outdoor applications.
- Microalloyed Steels: Include small amounts of niobium, vanadium, and titanium for grain refinement.
- Dual-Phase Steels: Feature a combination of martensite and ferrite phases for enhanced strength and ductility.
- Control-Rolled Steels: Mechanically processed to improve grain structure.
Applications
Automotive Industry: Frames, bumpers, and structural components.
Construction: Bridges, buildings, and offshore structures.
Energy Sector: Pipelines and pressure vessels.
Transportation: Railcars, shipping containers, and cranes.
Agricultural Equipment: Tractors and heavy machinery.
Advantages Over Traditional Carbon Steels
Higher strength-to-weight ratio.
Better corrosion resistance.
Lower weight without sacrificing performance.
Would you like further details on specific grades or processing techniques?